PROCESS
MADE IN A WORKSHOP, NOT A FACTORY
Every item we sell is made by our team of craftsmen right here in Southern CA. Each piece that leaves our shop is molded, cast, de-molded, diamond honed, cleaned, sealed, and detailed...all by hand
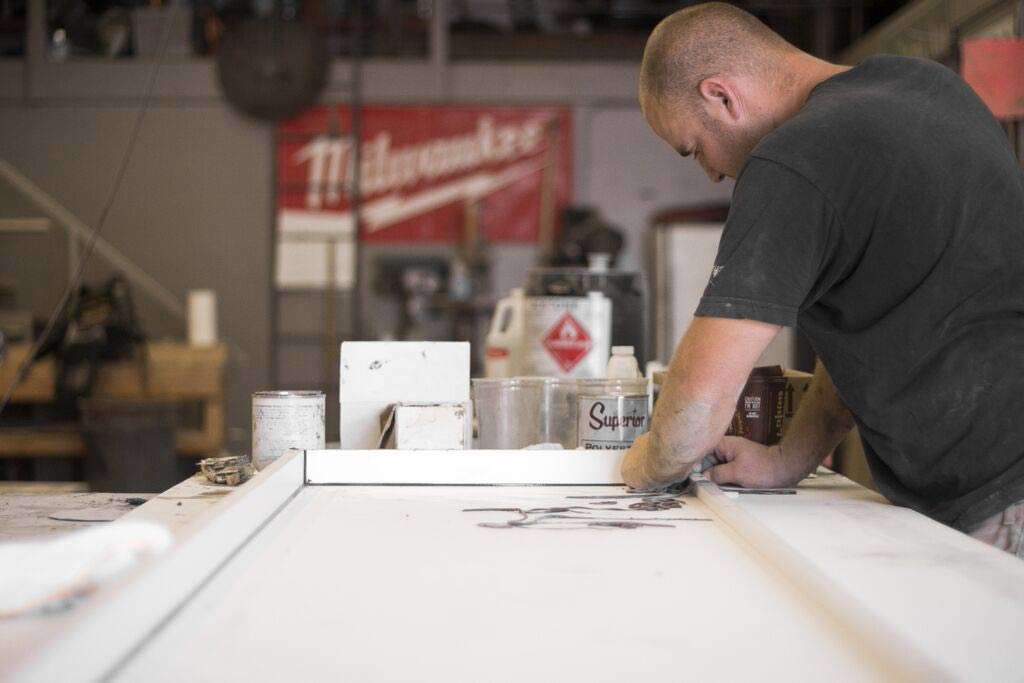
mold making
the shape
Each piece starts with a custom mold. From wood to fiberglass to spandex, we use just about anything we can get our hands on.
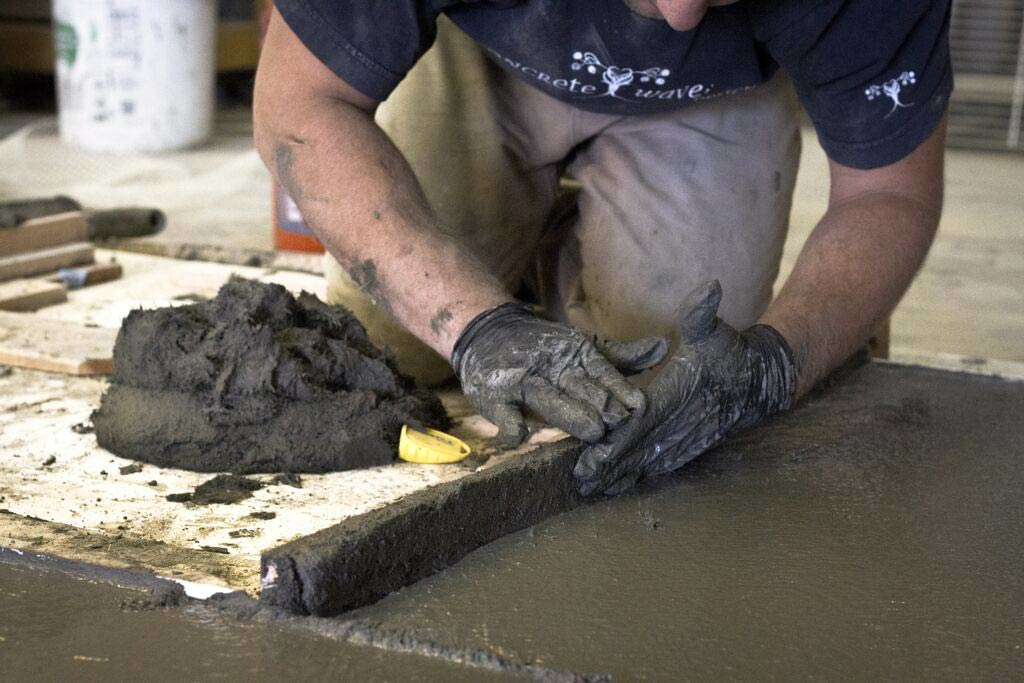
casting
the mess
Casting is controlled chaos. As much as we follow specific processes, concrete can throw a curveball. But that's what makes every piece a little different.
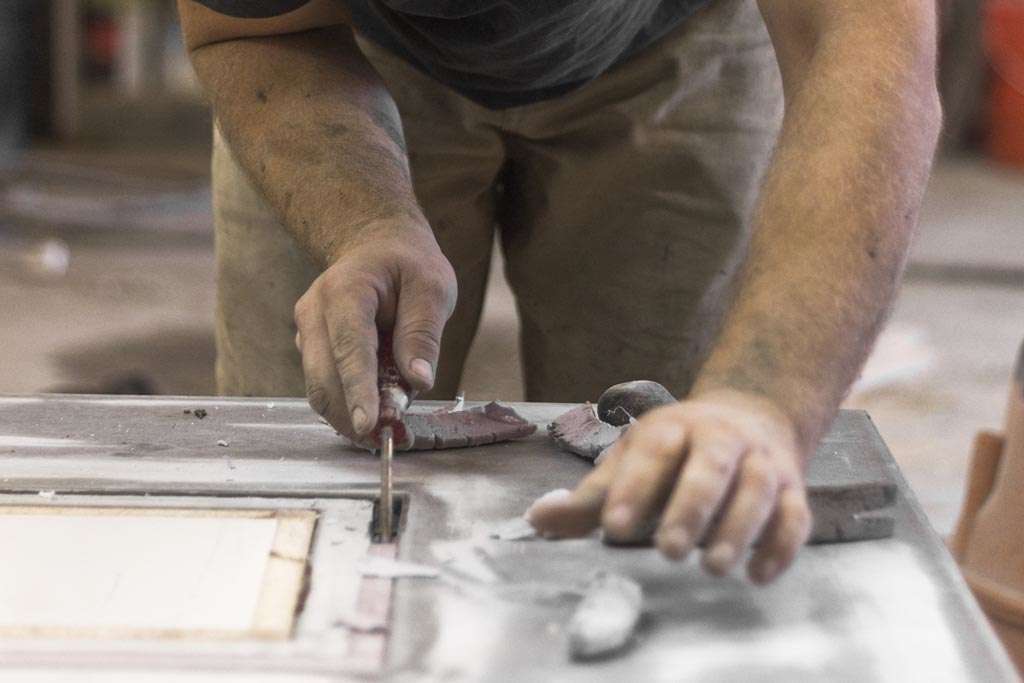
finishing
the details
Using diamond impregnated pads, we hone our pieces to smooth out any irregularities and bring out the true characteristics of the concrete.
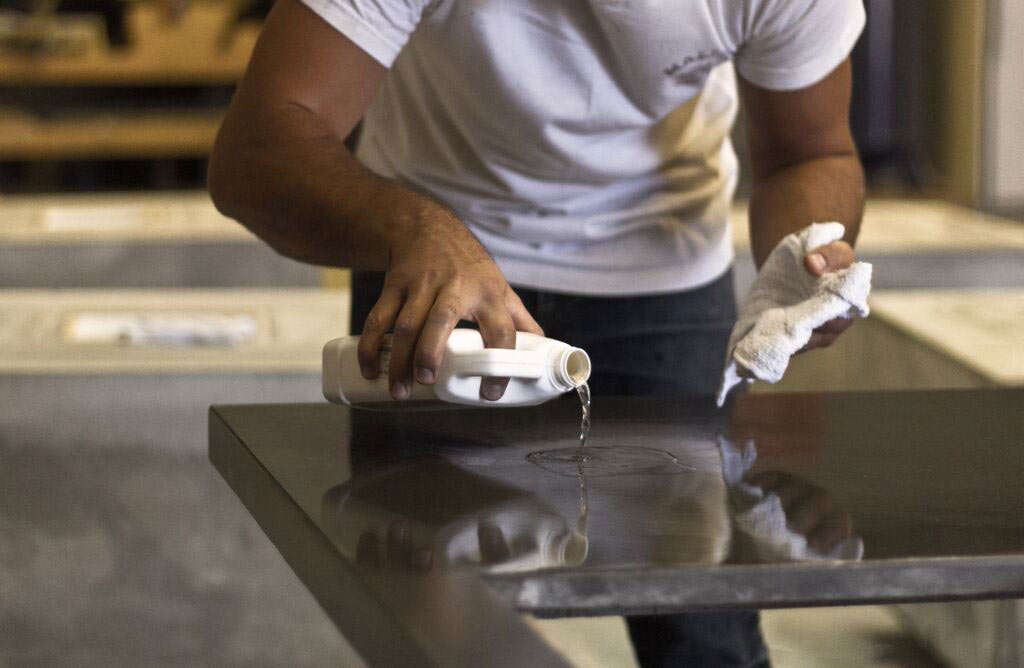
sealing
the protection
Our pieces then get fully sealed, ready to withstand full use. With normal use, this should be the very last time it gets sealed.
Color Samples
Ultra-Lightweight, Fiber-Reinforced Concrete
Lighter / Stronger / Better
Using our own mix of sand, cement, and recycled aggregates, we can achieve an ultra-lightweight mix that still maintains the true characteristics and features of traditional concrete. Doing this not only saves our backs, but it takes away a lot of design limitations of traditional concrete or stone. We're able to cast much larger pieces without having to seam pieces together or cast onsite.
Advantages
- Cast as thin as 3/8" (Typically 3/4" - 1" thick)
- 1/3 the weight of traditional concrete and 1/2 the weight of most natural stone
- Superior strength and flexibility over traditional concrete
- Excellent crack-resistance
- Great for complex 3-dimensional shapes
- Larger pieces without seams
- Real concrete, not a low-quality imitation or coating